Konsep lean manufacturing telah diperkenalkan di perusahaan-perusahaan Rusia belum lama ini, dibandingkan dengan negara-negara asing, di mana filosofi Kaizen mulai diterapkan pada 1950-an. Satu dekade lalu, hanya sepertiga perusahaan industri Rusia yang tertarik untuk mengoptimalkan produksi. Sekarang konstruksi sistem produksi yang efisien, selain produksi dan konsultasi industri yang terpisah, digunakan tidak hanya oleh perusahaan besar, tetapi juga perusahaan menengah di banyak sektor ekonomi.
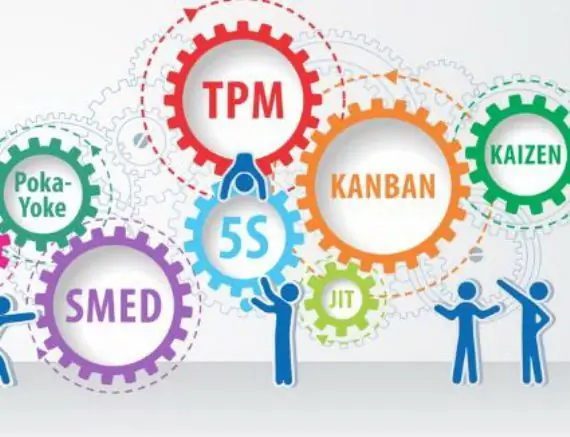
Nenek moyang sistem lean manufacturing adalah raksasa mobil Ford dan Toyota. Di antara perusahaan asing yang berhasil menerapkan prinsip-prinsip produksi Lean, seperti Nike, Textron, Parker, Intel. Awal penggunaan aktif teknologi Lean di negara kita dianggap tahun 2006, ketika Forum Lean Rusia Pertama berlangsung. Pelopor dalam penciptaan sistem produksi ramping domestik adalah produsen mobil terkenal kami - GAZ dan KAMAZ. Rusal, Rosatom, Eurochem, TVEL, Sberbank, dan banyak lainnya memimpin di antara perusahaan yang menggunakan sistem dan metode pengoptimalan Lean.
Implementasi logistik lean manufacturing di perusahaan Rusia mendapat dukungan negara dan diatur oleh standar utama: GOST bernomor R 57522-2017, R 57523-2017, R 57524-2017, serta rekomendasi industri yang disetujui oleh perintah Kementerian Perindustrian dan Perdagangan.
Istilah "Lean manufacturing" atau LIN adalah terjemahan semantik dari definisi bahasa Inggris "lean manufacturing", "lean production" dan transkripsi singkatannya LEAN.
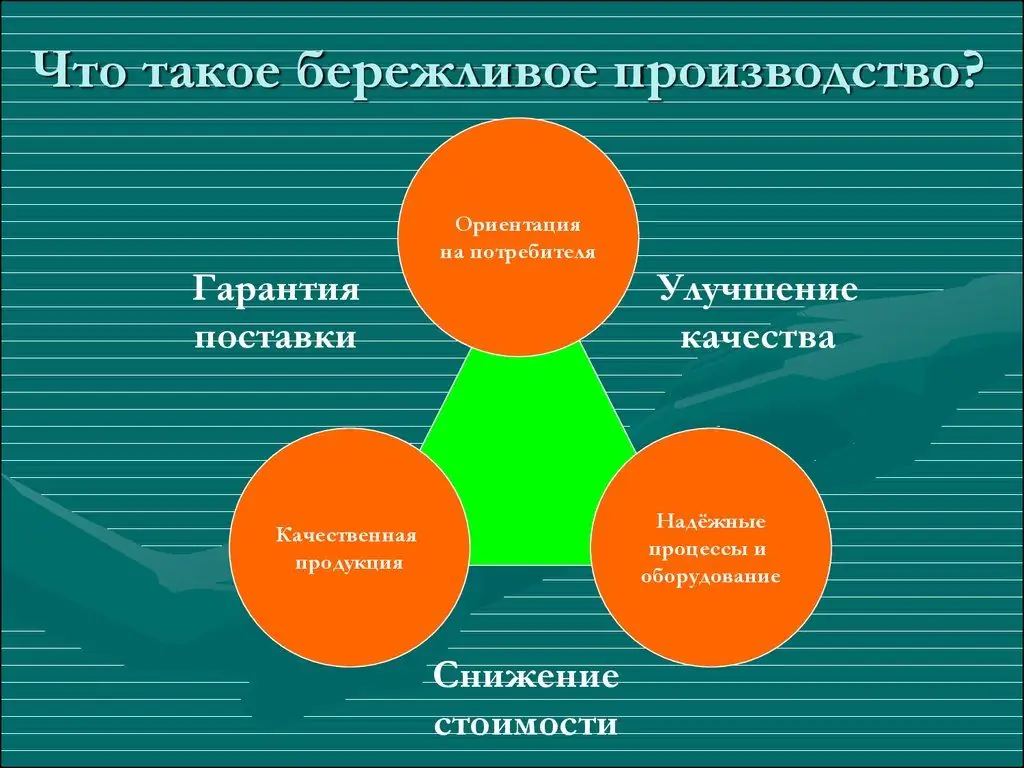
Lean manufacturing dipahami sebagai sistem manajemen perusahaan yang memungkinkan Anda meningkatkan kualitas kerja sekaligus mengurangi biaya dengan mengurangi kerugian.
Terjemahan Inggris-Rusia dari kata lean adalah "kurus, ramping, ramping". Untuk menjadi seperti itu, Anda perlu menghilangkan kelebihan lemak. Berkenaan dengan bidang produksi, ini berarti perlu untuk menghilangkan kerugian, sehingga mengurangi biaya. Oleh karena itu, lean manufacturing terkadang disebut lean.
Tiga konsep produksi LIN
Inti dari produksi Lean dijelaskan oleh G. Ford, yang mengatakan:.
Dalam sistem manufaktur Lean, dua aspek mendasar:
- Perlu melibatkan setiap karyawan perusahaan dalam prosedur optimasi.
- Perusahaan harus fokus secara maksimal pada kepentingan konsumen.
Secara konseptual, sistem optimasi produksi global didasarkan pada tiga prinsip.
- Filosofi Kaizen. Ini adalah mekanisme manajemen berdasarkan gagasan peningkatan kualitas berkelanjutan dan implementasinya secara operasional dan bertahap. Strategi Kaizen didasarkan pada pernyataan bahwa tidak ada batasan untuk perbaikan proses produksi dan setiap perusahaan, terlepas dari daya saingnya, harus bergerak maju.
- Konsep Six Sigma didasarkan pada fakta bahwa Anda dapat mengelola produksi menggunakan prinsip keterukuran data apa pun. Karena proses produksi diukur, mereka dapat dipantau, dan oleh karena itu ditingkatkan, dengan menganalisis, misalnya, KPI indikator kinerja utama. Konsep ini bertujuan untuk membuat semua proses produksi dapat diprediksi dan diprediksi, meningkatkan yang sudah ada dan membuat algoritma pengoptimalan baru.
- Meningkatkan efisiensi produksi, meningkatkan kualitas produk yang diproduksi, sekaligus mengurangi biaya - ini adalah tugas sistem Lean Manufacturing.
Secara bersama-sama, ketiga konsep ini menunjukkan bagaimana secara bertahap dan terus menerus meningkatkan kualitas proses produksi dan produk akhir tanpa menimbulkan biaya yang tidak perlu.
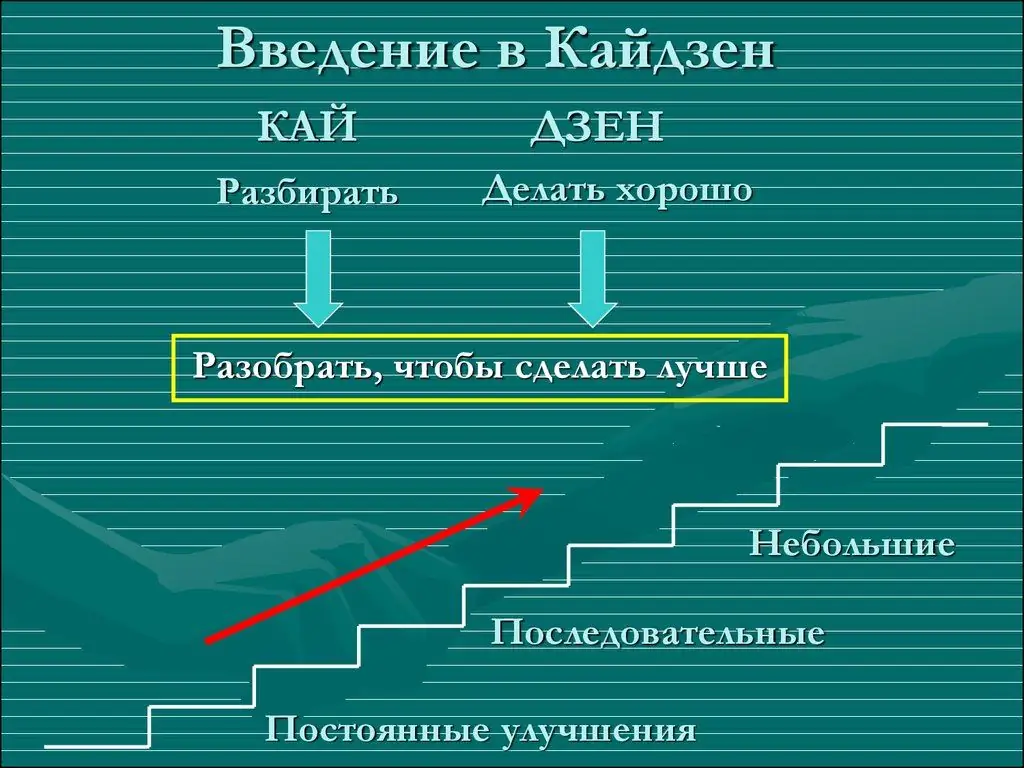
Dengan demikian, radikalisme dalam manajemen produksi telah digantikan oleh filosofi terintegrasi yang menggunakan prinsip-prinsip idealis metode liberal manajemen perusahaan dan menerapkan metodologi dan alat yang efektif untuk meningkatkan pekerjaan.
Alat ramping
Teknologi ramping digunakan di semua tahap kegiatan perusahaan - mulai dari desain awal proses produksi hingga penjualan produk ke konsumen.
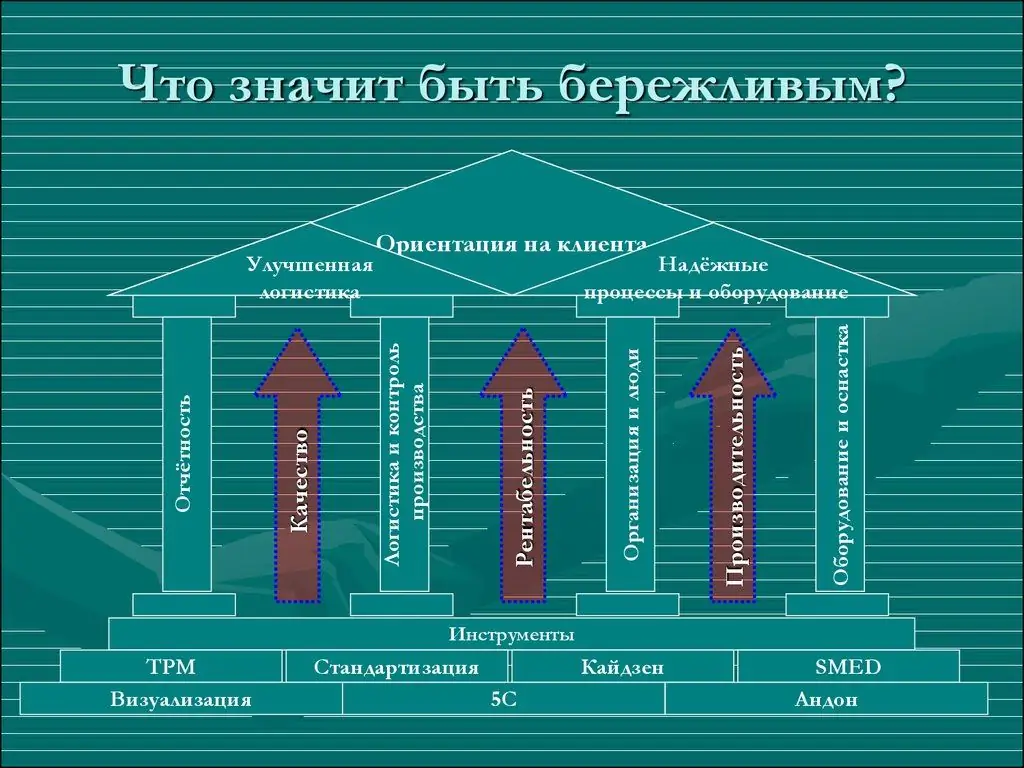
Proses optimasi berkelanjutan dilakukan menggunakan alat Lean:
- Total perawatan produktif peralatan - TPM (Total Productive Maintenance).
- Pergantian cepat dan retooling peralatan "dalam satu menit" dan "satu sentuhan" - SMED (Single Minute Exchange of Die) dan OTED (One Touch Exchange of Dies).
- Organisasi aliran material yang berkelanjutan - CANBAN.
- Tarik produksi - tarik produksi.
- Pemetaan aliran nilai - VSM (Pemetaan Aliran Nilai).
- Sistem manajemen material "tepat waktu" - JIT (Just-In-Time).
- Manajemen visual dan sistem umpan balik Andon.
- Standarisasi Pelaksanaan Pekerjaan - Standar SOP Proses Operasi.
- Teknologi untuk menciptakan tempat kerja yang efektif - 5S atau 5S -CANDO.
- Sistem manajemen mutu total - TQM (Total Quality Management).
Alat lean bekerja sedemikian rupa sehingga peningkatan kualitas pekerjaan dimaksimalkan dan dievaluasi pada semua tahap dan tingkat produksi.